Cutting-Edge Craft: 8 Times CNC Technology Redefined Modern Wooden Architecture
When machines take the wheel (or the blade), design gets sharper — literally. The post Cutting-Edge Craft: 8 Times CNC Technology Redefined Modern Wooden Architecture appeared first on Journal.
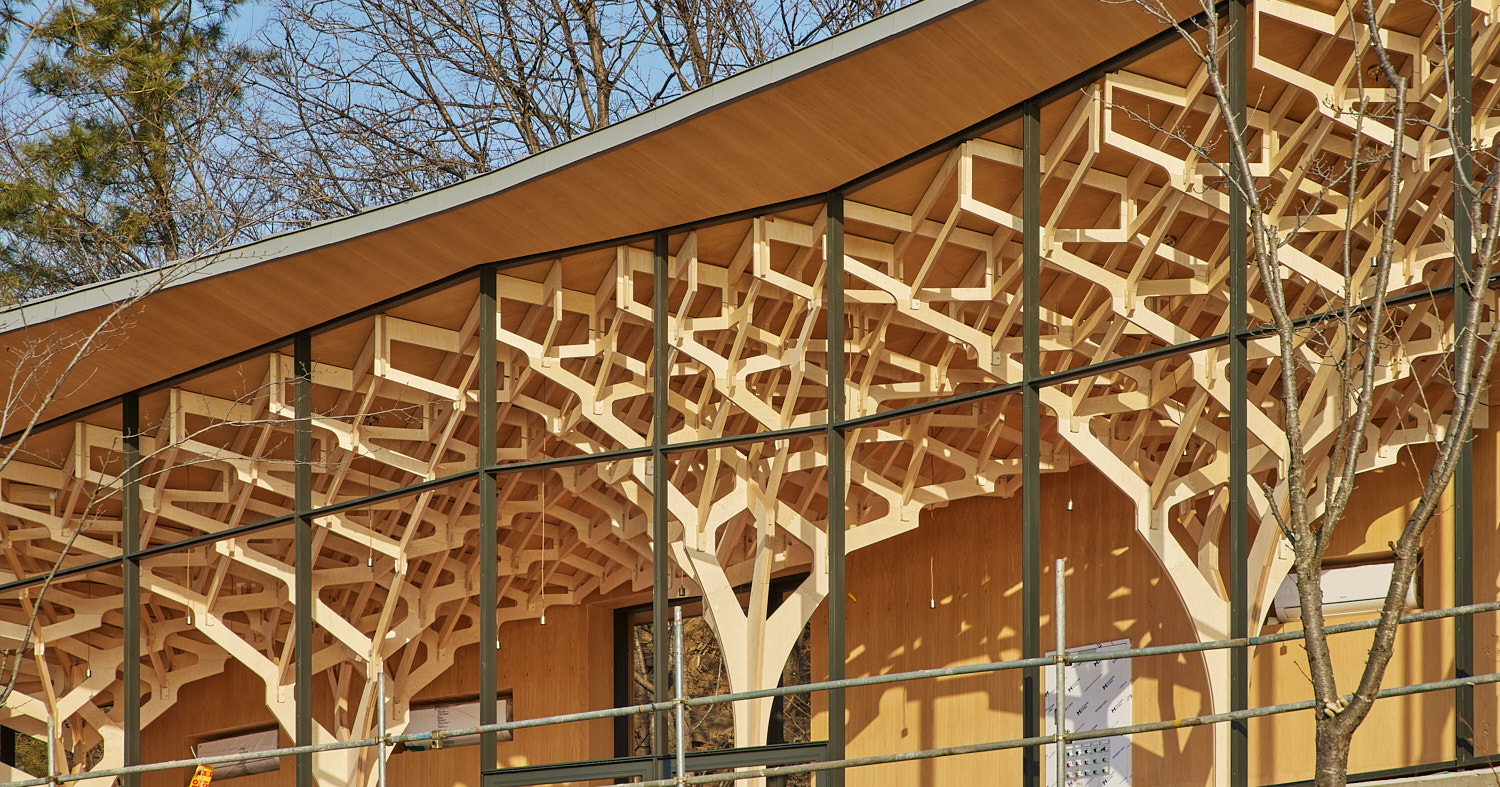
The countdown to 13th Annual A+Awards winners' announcement has begun! Stay updated by subscribing to Architizer's Awards Newsletter.
It’s safe to say that the days when architects relied solely on hand-drawn plans and traditional tools to bring their visions to life are long gone. Nowadays, they use a mix of advanced techniques, from parametric modeling to robotic fabrication. One of these tools is CNC (Computer Numerical Control) technology — a method that cuts, mills and carves materials with machine-guided precision. This allows architects to shape wood, metal, and even concrete with incredible accuracy, making intricate designs faster and more efficient to build.
While CNC is commonly used behind the scenes for cabinetry, structural elements or standardized components, some projects take it a step further, making the technology integral to the design and construction process. Whether carving out wooden lattices, constructing gravity-defying pavilions, or repurposing recycled materials, CNC technology can help turn complex ideas into reality. And for these eight projects, that’s precisely what it does.
The Learning Architecture for Learners
By VUILD, Koganei, Japan
This incubation center brings together industry, government and academia under a structure shaped by CNC precision. Using 5-axis CNC milling, three-dimensionally curved wood beams and panels were cut to serve as both concrete formwork and the final structural surface. Instead of being discarded, the wooden molds remain in place, giving the building its distinctive character. The shell’s depth is formed by a zigzag cross-section, with layers slightly offset to add strength. Every component was pre-cut in VUILD’s own factory, ensuring accuracy and efficiency. The result is a lightweight yet resilient structure that demonstrates how digital fabrication can minimize waste while pushing the possibilities of timber construction.
Pavilion of Floating Lights
By JK-AR, Jinju-si, South Korea
The Pavilion of Floating Lights reinterprets East Asian timber architecture through CNC precision and augmented reality. Inspired by the historic -ru pavilions, the structure features six tree-like columns that echo the wooden brackets of Chokseok-ru, a landmark built in 1365. Traditional carpentry techniques are revived without nails or adhesives, using CNC-milled plywood components assembled on-site with AR guidance. This approach increases construction efficiency while honoring heritage craftsmanship. Positioned along the Namgang River, the pavilion offers an open civic space for public gatherings, particularly during the Floating Lights Festival. Its delicate framework, combined with glass walls, creates a sense of openness, reconnecting visitors with the city’s natural and historical landscape.
Learning from Trees
By Andrew Barre Lab, Venice, Italy
Learning from Trees is a lightweight timber installation designed for the Italian Pavilion at the 2021 Venice Biennale. Built from 1.2 kilometers of CNC-milled timber, the structure forms a delicate lattice that appears woven but is precisely engineered for rapid assembly. Each timber piece was cut using a specialized CNC process that minimizes waste and eliminates the need for complex steel joints. The system relies on diamond-shaped profiles and hidden symmetries to simplify connections while maintaining structural strength. Originally part of a now-demolished state house, the reclaimed timber finds new life in this modular, low-carbon design. After the Biennale, the structure was disassembled without adhesives and is being permanently reinstalled in Italy, proving that precision fabrication can support both sustainability and reuse.
National Museum of Qatar Gift Shops
By KOICHI TAKADA ARCHITECTS, Qatar
Jury Winner, Retail, 8th Annual A+Awards
Inspired by the glowing gypsum crystals of Dahl Al Misfir, the National Museum of Qatar Gift Shops turn wood into an immersive sculptural experience. The design consists of 40,000 CNC-cut European oak pieces, each uniquely shaped to fit only in its precise location. Cut in Italy and assembled by hand in Qatar, the pieces were encoded with visual markers to guide their placement—like a massive three-dimensional puzzle. Without visible fixings, the structure forms a flowing, organic space that echoes the museum’s desert rose-inspired architecture. CNC technology allowed for extreme precision, transforming a complex concept into a tangible, functional interior that feels both intricate and natural.
IWI
By IWI Studio, Quito, Ecuador
IWI is a modular living space built with CNC-milled wood for precision, easy assembly and mass production. Designed to expand and contract, it shifts between a compact storage unit and a fully functional workspace, studio or relaxation area. The structure consists of two modules connected by a folding mechanism, allowing users to modify the space as needed. The back module acts as a built-in storage system with tables, chairs, shelves and essential utilities like lighting and water connections. The front module slides open, extending the accordion-like frame and fabric enclosure. CNC milling ensures every piece fits with accuracy, creating a flexible, efficient design that transforms spaces without wasting them.
Sauna in Teshikaga
By VUILD, Teshikaga, Japan
This tower-shaped sauna rethinks traditional bathhouse design through digital precision and advanced fabrication. Using a 5-axis CNC machine, solid cypress blocks were cut into free-form curves that shape both the interior and exterior. Each wooden piece is unique, designed to interlock with three-dimensional grooves that hold the structure together without traditional fasteners. Inside, a spiraling layout guides visitors through a gradual temperature shift, with warmth increasing as they ascend. Seating blocks double as structural supports, maximizing vertical space. Adjustable airflow and indirect lighting contribute to a controlled thermal experience. By merging CNC technology with ancient sauna principles, this project turns a simple ritual into an architectural journey of heat, light and form.
Cavilion
By Dahi Studio, Tehran, Iran
Cavilion is a bending-active pavilion built through CNC precision and computational design. Created as part of the DigiPy workshop, the project introduced students to digital fabrication, guiding them from concept to full-scale assembly. Using a 3-axis CNC machine, plywood components were cut with exacting accuracy, each piece uniquely shaped to fit into the pavilion’s flowing structure. Instead of relying on rigid frameworks, the design harnesses elastic deformation, allowing flat plywood strips to form a double-curved surface when assembled. Every part was labeled for easy construction, reducing complexity despite the intricate geometry. Built in just three days at the University of Tehran, Cavilion demonstrates how digital tools can streamline fabrication while embracing adaptability, efficiency and structural innovation.
Ashen Cabin
By HANNAH, Ashen Cabin
Ashen Cabin pushes digital fabrication to its limits, combining 3D-printed concrete with robotically milled wood to create a small but experimental structure. Its concrete foundation and walls are printed using a custom-built large-scale printer, forming corbeled surfaces that define key areas like seating, storage and a towering fireplace. The upper envelope, made from irregular ash logs, is cut with robotic precision to fit together despite their natural inconsistencies. This process turns wood once deemed waste — infested by the Emerald Ash Borer — into a durable and striking cladding system. By merging 3D scanning, CNC machining and robotic milling, Ashen Cabin rethinks traditional construction, proving that overlooked materials and cutting-edge technology can shape innovative architecture.
The countdown to 13th Annual A+Awards winners' announcement has begun! Stay updated by subscribing to Architizer's Awards Newsletter.
The post Cutting-Edge Craft: 8 Times CNC Technology Redefined Modern Wooden Architecture appeared first on Journal.